Defender 90 First Edition Issues
#21
#22

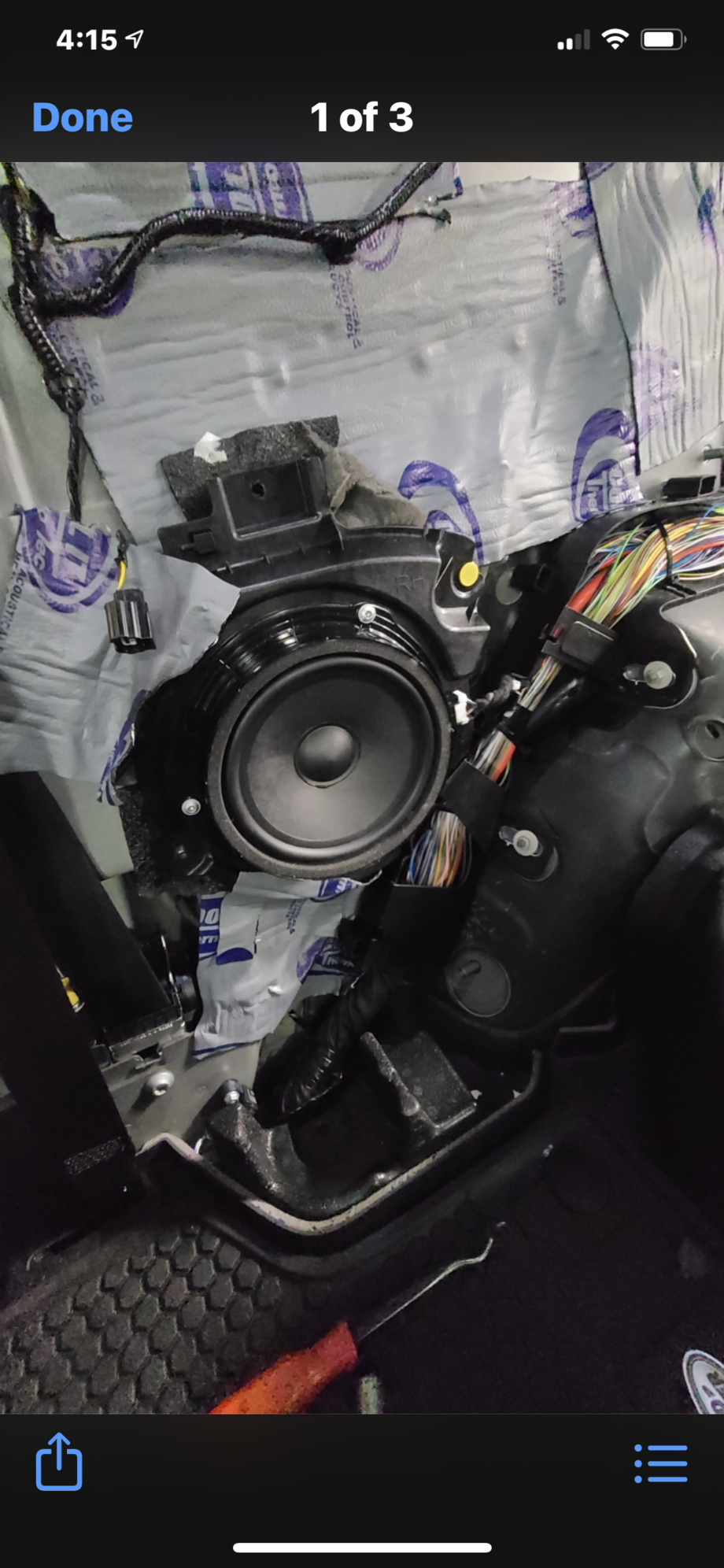
This is the silencing material that they tried on the last attempt…the other tape was there when the panels first came off…Does anyone else see the difference in the metal that runs along the window in mine vs vrovers? Mine looks like it was assembled by gorillas with hammers lol 😆
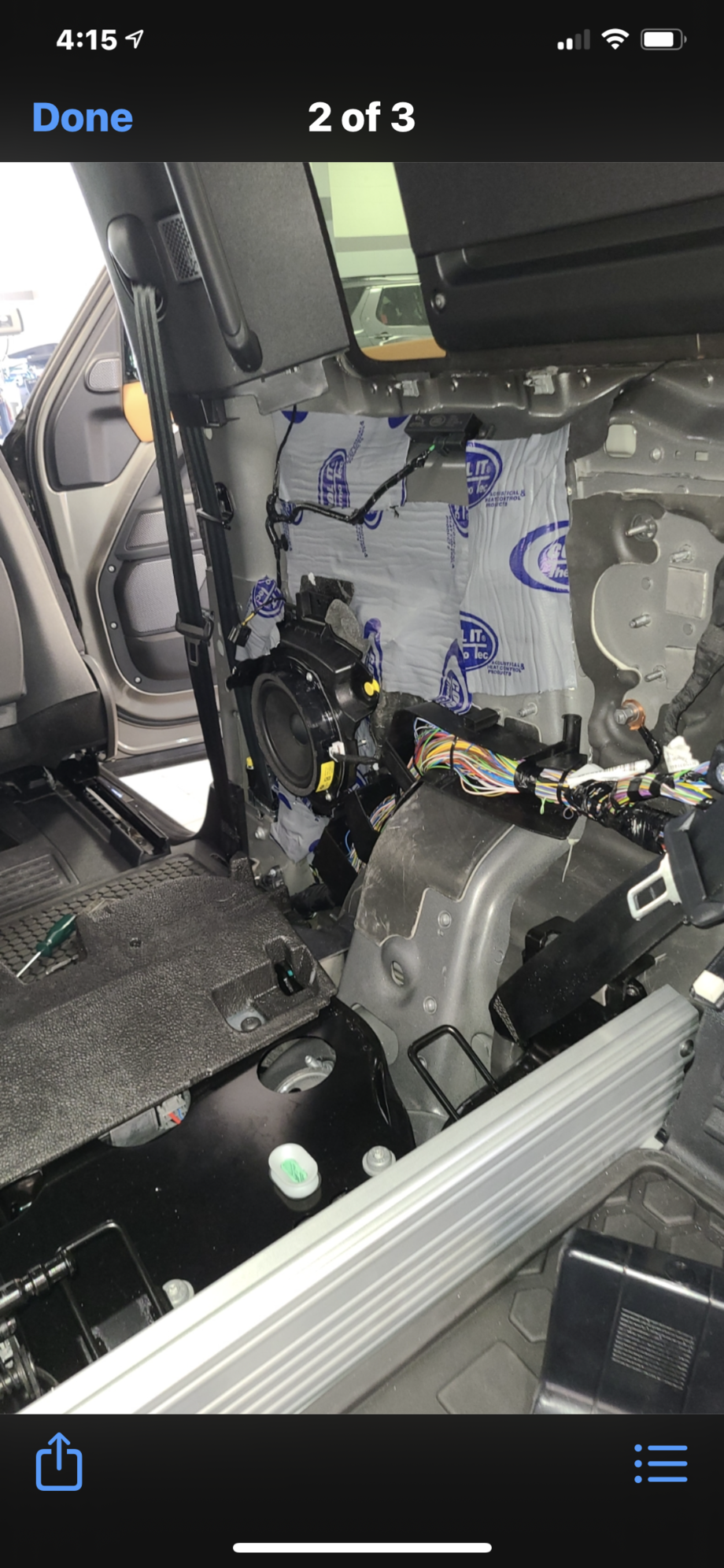
That area is aluminum right? When they say "welding" is the solution, they are talking about adhesive and not an actual weld?? If they do that bad of a job on the Dynamat, there is no way I'd let them try welding aluminium. It should go to a very qualified body shop for that.
The following users liked this post:
GFranklin (06-18-2021)
#23

Mine has a build date of 1/25/21 and was delivered to the dealer 3/12/21 and I have not noticed any abnormal rattles. I was getting an occasional noise from the back over certain surfaces that was remedied by adjusting my tailgate latch. Overall though the D90 is much tighter than the 2018 Discovery it replaced.
It looks like one of the D90s pictured above has the signature graphic in the back window (which mine does not have), not sure if that would be related to the noise? Hate to hear of others having issues.
It looks like one of the D90s pictured above has the signature graphic in the back window (which mine does not have), not sure if that would be related to the noise? Hate to hear of others having issues.
#24

This is so unacceptable and I feel bad for the owners who are having these issues. I am well aware that the first year of any model have significantly more issues than subsequent years, thus our decision to wait until 2021 for the 110's, which, other than the satellite nav issue, have been flawless. That said, why should, any manufacturer, especially one that deals in high end vehicles, have all these structural problems? Bad setting on the robot welders? Bad setting on the automatic glue application units? And, considering the thousands of 110's, why such an issue with the 90's? I sure hope you all ferret out the issues and hold JLR to the fire to fix or replace. Cheers and be safe and well.
The following users liked this post:
GFranklin (06-19-2021)
#25

Mine has a build date of 1/25/21 and was delivered to the dealer 3/12/21 and I have not noticed any abnormal rattles. I was getting an occasional noise from the back over certain surfaces that was remedied by adjusting my tailgate latch. Overall though the D90 is much tighter than the 2018 Discovery it replaced.
It looks like one of the D90s pictured above has the signature graphic in the back window (which mine does not have), not sure if that would be related to the noise? Hate to hear of others having issues.
It looks like one of the D90s pictured above has the signature graphic in the back window (which mine does not have), not sure if that would be related to the noise? Hate to hear of others having issues.
#26

Can I ask, do you have a 2021D90? And besides the graphic above do you see the inside of D90’s often enough to say it looks “normal” Well I’ve unfortunately had the pleasure of seeing mine on 4 different occasions, including the first time it was taken apart and I can assure you that this isn’t normal!! As the gentleman in a earlier post pointed out, you don’t just try to cover something up, you find it and fix it…I didn’t buy a mid $90K vehicle for it to be stuffed with foam, plastic, and covered in heat tape normally used in the engine bay or other high heat areas, which this is not…normal REALLY! Say it does need a spot weld or two, if that’s what it turns out to be. Would you be okay with heat tape instead if it was your car?
I realize that the area of metal below the window can’t be seen entirely in the picture, so if that’s what you mean by looking normal, I wish you could have seen it as I did…They actually stopped me from taking more pictures so I was only able to get these pics really quick…said it was some rule about pics and video in the service area???
I realize that the area of metal below the window can’t be seen entirely in the picture, so if that’s what you mean by looking normal, I wish you could have seen it as I did…They actually stopped me from taking more pictures so I was only able to get these pics really quick…said it was some rule about pics and video in the service area???
Last edited by GFranklin; 06-18-2021 at 01:37 PM.
#27

After all the attempts to fix the problems, I picked the D90X up on 5-7-21 after 16 days and the 4th try which unfortunately didn’t work either, but while there the lead service tech in the garage had told me that he had been checking out every D90 that came through the dealership, and he said that they all were having the same problem and he was going to open a ticket with JLR. I didn’t ask what exactly it meant but I assumed it was to let them know about the issue, and everything he done to try and fix it, but with no success…As I was driving home and realized it wasn’t fixed I called Sam the service advisor within 5 minutes of leaving the dealership and asked Sam what could we do next, and he said that we would have to have a conversation with the facilities manager, Jennifer because they had exhausted all they could do, and that they had informed JLR corporate, and then we were told that it could take some time for JLR corporate to come up with a universal fix that would work for any other one that had the same problem…Well after reaching out to Sam again yesterday to see if they had any news on it from JLR corporate, his response was baffling, because he said that it had not been escalated to JLR corporate yet, but he would talk to Jennifer about it again!! I guess it had slipped his mind that he had promised us that he would have it done right away…So for over a month now he has been telling us that he’s gotten no word back from JLR yet, and it should be very soon, and he was so grateful for our patience…WHEN HE NEVER DID IT TO BEGIN WITH!! Talk about feeling like just a number to them.. Thanks for letting me rant..! I’m just so truly disappointed and confused about it all…This was a purchase, not a lease and we waited and wanted this vehicle for so long, and it was going to be a keeper…we were 4th in line for ours only because employees got the first 3 slots, and the first D90 X…If anyone knows of any corporate contact info in the US that was responsive and helpful, it would be great if you could pass it on…my non forum email is bonairediver73@yahoo.com
Thanks,
sunny regards..!
Thanks,
sunny regards..!
#28

I don't know if this will help but I have a really odd background that includes managing a high-end custom car audio shop to owning a contracting firm that did commercial and residential audio, security, surveillance, etc. We very frequently had to fabricate things out of metal and I learned to weld and bond steel and aluminum. I've had years in construction and it has me looking at this maybe a little differently.
I understand you are incredibly upset and you should be. I would be.
But. I think this MIGHT be a simple problem that has been made much worse by a dealer that just has no idea what they are doing. Their sloppy work combined with terrible communication is making it unbearable. If they had a more experienced tech and a faster cleaner solution then you would have been on your way. We could debate that the dealers shouldn't be expected to solve these issues and that JLR should have a TSB by now similar to their a-pillar fix "put tape on it" or their improperly factory treated seat material (their words from the TSB) that says to "use a few liters of water and a shop vac to clean it".
Sorry for getting off-topic but it seems like the real problem here is corporate incompetence and a "patch it" or "cover it up" culture.
Looking at your pictures, the sound deadening material (adhesive sheets / Dynamat) is not intended to be used that way.
It's designed to deal with resonant frequency problems (vibrations). Overly simplified, every part in the car has a frequency where it vibrates which can lead to noise. When a car goes into a good custom audio shop for some upgrades, one final step is to play a test disc to find and eliminate any vibrations. The disc plays test sweeps. It starts at sub-audible bass and slowly plays every frequency all the way to piercing highs. It sounds similar to the sweep you hear at the start of a THX movie but with a larger range and less stylized. While the sweep plays, you'll find that a license plate almost always rattles and there will be a couple of plastic parts, a trunk lid, or some random metal parts that make noise only at very certain frequencies. This is where the Dynamat comes in. It gets stuck on the back of these parts so that, when your favorite k-pop band hits one of those specific frequencies, the parts don't rattle.
Dynamat is not supposed to be a fix for parts that are rubbing together or parts that were not properly attached. It isn't glue, it does not "connect", "attach", or "secure". It only absorbs vibrations and deadens the material to eliminate noise.
Now we have a dealer sticking it on a car that "wasn't welded" properly?? Something is missing here. Is this a structural issue? Is this an adhesive joint or weld that has failed? Is this a design problem? If so, Dynamat is not the answer.
The other possibility is that it IS a structurally sound design that isn't failing but that a couple of metal parts are rubbing and it's just a nuisance. If this is the case, Dynamat is still not the answer. The parts need to be joined, altered, or separated (depending on the problem). This is where a couple of tack welds or an adhesive bond maybe with some rivets at the joint would solve the problem without reducing the safety or value of the car.
If you really want a solution, they need to take the Dynamat off, find the parts that are rubbing, figure out what really went wrong, and actually fix it.
You would probably love this car if they did that on the first visit but it seems like their incompetence has spoiled the whole thing.
Sorry for the really long post but I hope it helps in some way.
I understand you are incredibly upset and you should be. I would be.
But. I think this MIGHT be a simple problem that has been made much worse by a dealer that just has no idea what they are doing. Their sloppy work combined with terrible communication is making it unbearable. If they had a more experienced tech and a faster cleaner solution then you would have been on your way. We could debate that the dealers shouldn't be expected to solve these issues and that JLR should have a TSB by now similar to their a-pillar fix "put tape on it" or their improperly factory treated seat material (their words from the TSB) that says to "use a few liters of water and a shop vac to clean it".
Sorry for getting off-topic but it seems like the real problem here is corporate incompetence and a "patch it" or "cover it up" culture.
Looking at your pictures, the sound deadening material (adhesive sheets / Dynamat) is not intended to be used that way.
It's designed to deal with resonant frequency problems (vibrations). Overly simplified, every part in the car has a frequency where it vibrates which can lead to noise. When a car goes into a good custom audio shop for some upgrades, one final step is to play a test disc to find and eliminate any vibrations. The disc plays test sweeps. It starts at sub-audible bass and slowly plays every frequency all the way to piercing highs. It sounds similar to the sweep you hear at the start of a THX movie but with a larger range and less stylized. While the sweep plays, you'll find that a license plate almost always rattles and there will be a couple of plastic parts, a trunk lid, or some random metal parts that make noise only at very certain frequencies. This is where the Dynamat comes in. It gets stuck on the back of these parts so that, when your favorite k-pop band hits one of those specific frequencies, the parts don't rattle.
Dynamat is not supposed to be a fix for parts that are rubbing together or parts that were not properly attached. It isn't glue, it does not "connect", "attach", or "secure". It only absorbs vibrations and deadens the material to eliminate noise.
Now we have a dealer sticking it on a car that "wasn't welded" properly?? Something is missing here. Is this a structural issue? Is this an adhesive joint or weld that has failed? Is this a design problem? If so, Dynamat is not the answer.
The other possibility is that it IS a structurally sound design that isn't failing but that a couple of metal parts are rubbing and it's just a nuisance. If this is the case, Dynamat is still not the answer. The parts need to be joined, altered, or separated (depending on the problem). This is where a couple of tack welds or an adhesive bond maybe with some rivets at the joint would solve the problem without reducing the safety or value of the car.
If you really want a solution, they need to take the Dynamat off, find the parts that are rubbing, figure out what really went wrong, and actually fix it.
You would probably love this car if they did that on the first visit but it seems like their incompetence has spoiled the whole thing.
Sorry for the really long post but I hope it helps in some way.
The following 2 users liked this post by _Allegedly:
GFranklin (06-19-2021),
Magnumforc (06-20-2021)
#29

Finally, we got an update from the service department and picked up our car yestersay evening. Here's the turn of events -
1. Asked the service manager what exactly the problem was and what they've done to fix it, just fyi - we've asked multiple times to call us, so we can drop by and take a look at the actual issue and the fix they've done. But yeah, unfortunately this wasn't the case and we've been left in the dark on whats being done at the body shop.
2. Previously (3 weeks back), the only update we had was that the vehicle was being sent to the body shop for some spot welding fixes (I have a text message stating the same). The reason they stated was that - sheet-metals were overlapping against each other, thereby leading to constant rattles and vibrations ( happens around B and C pillars).
3. When we went to pick up the car, the service manager now states that they couldn't get the weld done and they just put in some felt or dampening material between the sheet-metals and panels - we are so baffled and not sure why this would take three weeks.
4. We once again asked him what the underlying reason was, just trying to get a verbal commitment of the problem and here's his version - sheet-metal on left side of the car is actually overlapping and the gap between them isn't consistent, especially when comparing to the other side. He also said that they could hear it happen when they put some pressure on the cars external panels.
5. After some digging, we were able to locate the body shop where they sent the car to. We got in touch with the body shop technician and this is his version - theres definitely something weird going on around the B pillars of the car, they weren't sure what it is or wouldn't provide any further comment. When we inquired about spot welding (just because the service-manager previously told us that they need to spot weld) - they told us that they can't actually weld them due to the aluminum construction - at this point i don't have complete context into why or what as I don't build/repair cars for a living.
6. The gentleman just asked us to bring the car back if the issues persists.
7. We drove the car around for about 50 miles, just to check if the issues persist and to our tough luck they are all back.
8. Constant rattles and vibrations from the B and C pillars. In addition to this some of the interior plastic panels weren't put back properly - this will be an issue each time they open the back apart.
Here's a quick video -
PS - These problems are much more worse than what you can hear in the video. I also wondering how bad it would turn, if we really take this vehicle out off-road.
1. Asked the service manager what exactly the problem was and what they've done to fix it, just fyi - we've asked multiple times to call us, so we can drop by and take a look at the actual issue and the fix they've done. But yeah, unfortunately this wasn't the case and we've been left in the dark on whats being done at the body shop.
2. Previously (3 weeks back), the only update we had was that the vehicle was being sent to the body shop for some spot welding fixes (I have a text message stating the same). The reason they stated was that - sheet-metals were overlapping against each other, thereby leading to constant rattles and vibrations ( happens around B and C pillars).
3. When we went to pick up the car, the service manager now states that they couldn't get the weld done and they just put in some felt or dampening material between the sheet-metals and panels - we are so baffled and not sure why this would take three weeks.
4. We once again asked him what the underlying reason was, just trying to get a verbal commitment of the problem and here's his version - sheet-metal on left side of the car is actually overlapping and the gap between them isn't consistent, especially when comparing to the other side. He also said that they could hear it happen when they put some pressure on the cars external panels.
5. After some digging, we were able to locate the body shop where they sent the car to. We got in touch with the body shop technician and this is his version - theres definitely something weird going on around the B pillars of the car, they weren't sure what it is or wouldn't provide any further comment. When we inquired about spot welding (just because the service-manager previously told us that they need to spot weld) - they told us that they can't actually weld them due to the aluminum construction - at this point i don't have complete context into why or what as I don't build/repair cars for a living.
6. The gentleman just asked us to bring the car back if the issues persists.
7. We drove the car around for about 50 miles, just to check if the issues persist and to our tough luck they are all back.
8. Constant rattles and vibrations from the B and C pillars. In addition to this some of the interior plastic panels weren't put back properly - this will be an issue each time they open the back apart.
Here's a quick video -
Last edited by vrover90; 06-19-2021 at 12:18 PM.
The following users liked this post:
GFranklin (06-19-2021)
#30

Aluminum "can" be welded but it is incredibly difficult. It mostly just melts and falls apart. Only an extremely experienced tech should attempt. Even done well, it's a less desirable fix.
I'll double down that the TSB will eventually be "remove paint, apply 2-part flexible adhesive within 10 minutes, repaint".
It will not be "jam felt pads into the problem".
It might sound crazy but adhesive is an ideal fix. Modern aircraft assembly relies extensively on adhesives. Rivets and welds are less reliable and can become corrosion points so they're being eliminated as much as possible.
The following 3 users liked this post by _Allegedly: