Rust: Part II
#1

Ok, for the uninitiated, this is the fix thread for my https://landroverforums.com/forum/di...=rust+thoughts thread.
Setup:
- Wire-sanded rusted areas, and then gave them a good dousing with this stuff
It has a nice foaming action that makes it appear to work better than the permatex and rustoleum rust converters. Probably just a placebo-effect thing, but oh well.
- Picked up a lincoln weld-pak 100 and an auto dim helmet for $250 off craigslist
. See the bottom dial? Apparently, it is very helpful that your welder have adjustable voltage like that when doing sheet metal.
- Jake estimated the body frame thickness at about 20ga, which I think is about right. Home Depot, Lowes, Menards etc. only carry 16ga and 22ga, so I got a couple sheets of each thickness (16 for structural, 22 for covering holes).
- As a complete welding newbie, I then did a bunch of reading. The following
sites are very helpful:
MIG Welding - The DIY Guide
WeldingWeb™ - Welding forum for pros and enthusiasts - Powered by vBulletin
Miller - Improving Your Skills - MIG Welding
These were supplimented by more specific google searches which would usually lead to old hot-rod, mustang, and dodge sites. The old dudes in the forums there will also have some good tips.
From here, I had about 2 hours of practice, then pretty much had to just jump into it. I had to move out of my old place on the 30th, and my new place doesnt allow "major" automotive repairs, so I had to learn and do very quickly.
pics in next post
Setup:
- Wire-sanded rusted areas, and then gave them a good dousing with this stuff

It has a nice foaming action that makes it appear to work better than the permatex and rustoleum rust converters. Probably just a placebo-effect thing, but oh well.
- Picked up a lincoln weld-pak 100 and an auto dim helmet for $250 off craigslist
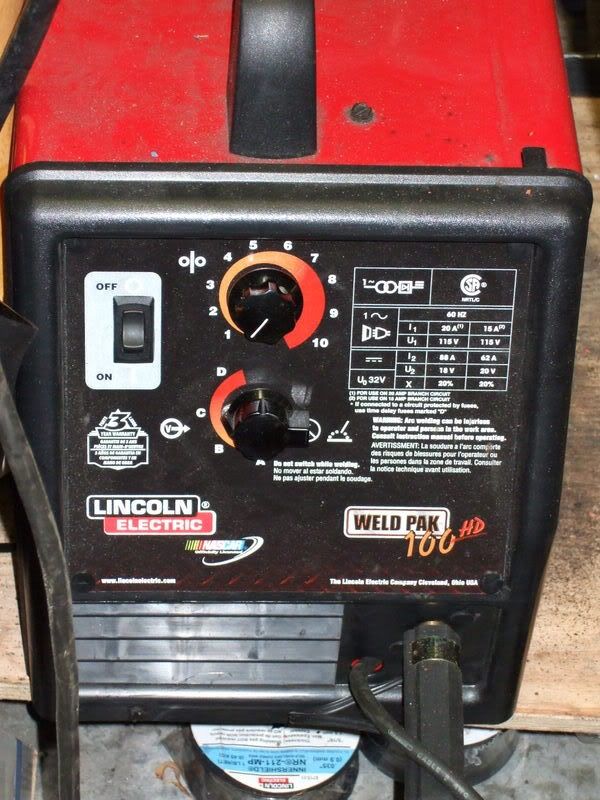
- Jake estimated the body frame thickness at about 20ga, which I think is about right. Home Depot, Lowes, Menards etc. only carry 16ga and 22ga, so I got a couple sheets of each thickness (16 for structural, 22 for covering holes).
- As a complete welding newbie, I then did a bunch of reading. The following
sites are very helpful:
MIG Welding - The DIY Guide
WeldingWeb™ - Welding forum for pros and enthusiasts - Powered by vBulletin
Miller - Improving Your Skills - MIG Welding
These were supplimented by more specific google searches which would usually lead to old hot-rod, mustang, and dodge sites. The old dudes in the forums there will also have some good tips.
From here, I had about 2 hours of practice, then pretty much had to just jump into it. I had to move out of my old place on the 30th, and my new place doesnt allow "major" automotive repairs, so I had to learn and do very quickly.
pics in next post
#2

I apologize for the quality and small number of pictures. It was 95+ degrees while I was doing this, and I was in a hurry.
I put the welder on B voltage and 1.5 wire speed. Tack welded around to get the sheet to stay in place. When I got 2 tacks within an inch of each other, I ran a string bead to connect them. I actually found it easier to connect the tacks than to make the tacks themselves.
Drivers Floor:
Used the 22ga sheet.

I put the welder on B voltage and 1.5 wire speed. Tack welded around to get the sheet to stay in place. When I got 2 tacks within an inch of each other, I ran a string bead to connect them. I actually found it easier to connect the tacks than to make the tacks themselves.
Drivers Floor:
Used the 22ga sheet.


Last edited by pinkytoe69; 07-05-2012 at 11:36 AM.
#3

Any of you with rust down the A post might want to pull your fender...
For these parts, I sanded them down, gave them the rust spray, welded in the patches, then sprayed again, then siliconed.
Used the 16ga sheet.
I dont have pics of each side in sequence, so the sequence is a combination of both





For these parts, I sanded them down, gave them the rust spray, welded in the patches, then sprayed again, then siliconed.
Used the 16ga sheet.
I dont have pics of each side in sequence, so the sequence is a combination of both







#4

Still got the passenger floor and the left rear cargo panel to do along with little things like the hole in the rear door/fender that everyone seems to get.
Would like to give thanks to Jake and Mountain Goat (and maybe 1 or two others I am forgetting) for pushing me to get a welder and do this stuff myself!
I probably only have quality welds at about a 60-70% rate, but thats good enough for this application, and I am continually improving. Having this skill (not that I am all that skilled yet) opens up so many automotive repair and modification avenues...its pretty cool
Also, for fellow beginners, dont be scared off by flux-core welding naysayers. There are no gas bottles or carts to wield about, which is nice. Yeah, brushing off the flux after every weld is a little annoying, but its not that bad. Dont be afraid to get your face in close, and the smoke will not be an issue in terms of seeing the puddle. Also, you can weld on rusty metal with it.
Would like to give thanks to Jake and Mountain Goat (and maybe 1 or two others I am forgetting) for pushing me to get a welder and do this stuff myself!
I probably only have quality welds at about a 60-70% rate, but thats good enough for this application, and I am continually improving. Having this skill (not that I am all that skilled yet) opens up so many automotive repair and modification avenues...its pretty cool

Also, for fellow beginners, dont be scared off by flux-core welding naysayers. There are no gas bottles or carts to wield about, which is nice. Yeah, brushing off the flux after every weld is a little annoying, but its not that bad. Dont be afraid to get your face in close, and the smoke will not be an issue in terms of seeing the puddle. Also, you can weld on rusty metal with it.
Last edited by pinkytoe69; 07-05-2012 at 11:56 AM.
#7

Thanks!
Im only about half done, but, yes, very pleased with what is done so far.
some tips/info:
- Trying to weld spots around the brake and gas pedals SUCKS. Its hard to hold the gun at the right angle, it is hard to get your face close enough to see the puddle, and you have no idea if the sheet has good contact at the spot you are about to weld on. Get a good feel for penetration timing and your technique before doing stuff around this area as you are pretty much flying blind.
- The undercoating will smolder and can catch on fire (usually if you get a burn through). Not a big deal...welding gloves are pretty hearty. I just smothered/taped it out with my hands.
- Dont be intimidated by vertical or upside-down welding. Its pretty much the same as doing a horizontal weld. Just keep the gun angle about 20 degrees from "vertical" and watch the puddle.
- since this is pretty thin sheet metal, a weave bead is unnecessary. You can just slowly pull the puddle and make a string bead.
Im only about half done, but, yes, very pleased with what is done so far.
some tips/info:
- Trying to weld spots around the brake and gas pedals SUCKS. Its hard to hold the gun at the right angle, it is hard to get your face close enough to see the puddle, and you have no idea if the sheet has good contact at the spot you are about to weld on. Get a good feel for penetration timing and your technique before doing stuff around this area as you are pretty much flying blind.
- The undercoating will smolder and can catch on fire (usually if you get a burn through). Not a big deal...welding gloves are pretty hearty. I just smothered/taped it out with my hands.
- Dont be intimidated by vertical or upside-down welding. Its pretty much the same as doing a horizontal weld. Just keep the gun angle about 20 degrees from "vertical" and watch the puddle.
- since this is pretty thin sheet metal, a weave bead is unnecessary. You can just slowly pull the puddle and make a string bead.
#8
Join Date: Mar 2010
Location: Pittsburgh PA suburbs.
Posts: 5,584
Likes: 0
Received 7 Likes
on
7 Posts

Not so sure I agree with the statement that you can weld rustry metal????
Lincoln is a good brand name welder and having the adjustability allows you to use it on a larger variety of thicknesses. It is great to be able to do your own welding. I took a basic welding course when I was in college at Southern Tech but never went beyond that with it.
Lincoln is a good brand name welder and having the adjustability allows you to use it on a larger variety of thicknesses. It is great to be able to do your own welding. I took a basic welding course when I was in college at Southern Tech but never went beyond that with it.
#9
#10

No, the flux takes the place of the shielding gas. all electric welding has to have some method to remove oxygen from the weld or it doesn't work. At least I've never been able to weld to rust over the 40+ years I've been doing it. What the flux core (and arc welding) does is penetrate through mild surface rust, but you can do the same thing with gas shielding by turning up the amperage.
Last edited by Bkreutz; 07-05-2012 at 04:43 PM.