Doing connection rod bearings
#1

I am considering doing the connection rod bearings, I have a pretty good hot idle (206 deg +) tick. Does anyone know of good write or can give me an idea of how much work I am looking at. It looks pretty straight forward, except for how common is to have fit an up sized bearing.
Heavier oil and getting my cooling re-sorted will correct some of it but if I have time and it is not too bad to do on a warm summer day or 2, I can get that eliminated.
Heavier oil and getting my cooling re-sorted will correct some of it but if I have time and it is not too bad to do on a warm summer day or 2, I can get that eliminated.
#2

Bearing size should match your crank. Machine your crank .010 and you need .010 upsized bearings.
Chock block your wheels, Disco in Neutral, engine off.
Drain oil. Drop oil pan (typically but not always easier to remove horizontal cross brace for this step).
Remove your oil pickup tube and clean it, check it for full flow. Easy. Fast. Just pour oil through it.
Remove your spark plugs (to make turning the motor by hand easier). Being in Neutral also helps.
Do one connecting rod at a time so that you never move rod end caps to a different cylinder. Remove the bottom cap half. Use your finger to slide out the old lower half of the connection rod bearing. View it for abnormal wear. Use it to push up on the upper half of the connection rod bearing so that it slides around the top of the crank down to where you can grab it or it drops. View it for abnormal wear. Now decide if you are going to hand clean that whole circular exposed race of the crankshaft.
With 100% surgically clean hands and a clean crankshaft (your call), put a drop of oil ONLY on the inside of the new upper connection rod bearing and push it up around the top half of the crank. Add a drop of oil to only the inside of the lower connection rod bearing and install that new part into the lower connection rod cap. Your lower or upper connecting rod cap may have a tiny cutout for one half of your upper/lower connection rod bearings to insert and thereby lock 1 tab. If so, insure that your connection rod bearing half has its tab correctly oriented such that it fits into the OEM connecting rod cap slot to prevent it from rotating around the crank. Remember, the crank turns inside these bearings... the bearings themselves do not turn. They are motionless unless you screw them up (aka "spun bearing").
Reinstall the lower connecting rod cap half. Remind yourself that you did NOT put any oil on the outside of either new bearing that touches the rod caps, and that only clean new oil went on the inside of your new bearings where they wrap around (essentially touch the surface of) the crank. You want friction on the outside of the bearings, no friction on their insides).
Repeat for any of the other rod caps that you can reach until finally your need to turn the motor by hand to reach others. Turn the motor by hand as needed and finish all other connecting rod bearings.
With all 8 rods finished, turn the motor by hand one last (but full) time to insure that your new bearings haven't locked up the motor (no harm if you catch and fix such a problem at this stage!).
Reinstall oil pickup tube with new gasket.
Reinstall oil pan.
Add oil.
Start motor. Look for leaks and listen for any suspicious metal on metal noises.
Done.
Budget 1 hour per rod bearing and 4 hours for pan/oil change/misc. 12 hour job with no access to power tools (hand tools only for my limited experience).
Chock block your wheels, Disco in Neutral, engine off.
Drain oil. Drop oil pan (typically but not always easier to remove horizontal cross brace for this step).
Remove your oil pickup tube and clean it, check it for full flow. Easy. Fast. Just pour oil through it.
Remove your spark plugs (to make turning the motor by hand easier). Being in Neutral also helps.
Do one connecting rod at a time so that you never move rod end caps to a different cylinder. Remove the bottom cap half. Use your finger to slide out the old lower half of the connection rod bearing. View it for abnormal wear. Use it to push up on the upper half of the connection rod bearing so that it slides around the top of the crank down to where you can grab it or it drops. View it for abnormal wear. Now decide if you are going to hand clean that whole circular exposed race of the crankshaft.
With 100% surgically clean hands and a clean crankshaft (your call), put a drop of oil ONLY on the inside of the new upper connection rod bearing and push it up around the top half of the crank. Add a drop of oil to only the inside of the lower connection rod bearing and install that new part into the lower connection rod cap. Your lower or upper connecting rod cap may have a tiny cutout for one half of your upper/lower connection rod bearings to insert and thereby lock 1 tab. If so, insure that your connection rod bearing half has its tab correctly oriented such that it fits into the OEM connecting rod cap slot to prevent it from rotating around the crank. Remember, the crank turns inside these bearings... the bearings themselves do not turn. They are motionless unless you screw them up (aka "spun bearing").
Reinstall the lower connecting rod cap half. Remind yourself that you did NOT put any oil on the outside of either new bearing that touches the rod caps, and that only clean new oil went on the inside of your new bearings where they wrap around (essentially touch the surface of) the crank. You want friction on the outside of the bearings, no friction on their insides).
Repeat for any of the other rod caps that you can reach until finally your need to turn the motor by hand to reach others. Turn the motor by hand as needed and finish all other connecting rod bearings.
With all 8 rods finished, turn the motor by hand one last (but full) time to insure that your new bearings haven't locked up the motor (no harm if you catch and fix such a problem at this stage!).
Reinstall oil pickup tube with new gasket.
Reinstall oil pan.
Add oil.
Start motor. Look for leaks and listen for any suspicious metal on metal noises.
Done.
Budget 1 hour per rod bearing and 4 hours for pan/oil change/misc. 12 hour job with no access to power tools (hand tools only for my limited experience).
The following 5 users liked this post by No Doubt:
boston4 (04-23-2020),
mollusc (04-23-2020),
Richard Gallant (04-23-2020),
Sixpack577 (04-23-2020),
whowa004 (04-23-2020)
#3

You may notice some pressure on the top half of the old connection rod bearings, but with the spark plugs removed and with the lower rod cap half removed you simply push that connecting rod+piston up a bit by hand and then you should have no pressure on the top bearing half to make removal easy, then just pull the connecting rod+piston back down onto the new upper bearing half.
*all that said, this whole job is really more useful for repairing rod knock than for fixing any ticks at idle
*all that said, this whole job is really more useful for repairing rod knock than for fixing any ticks at idle
#4

You might also consider replacing the main crankshaft bearings at the same time. You do need to have all the rod caps removed concurrently for that though. Careful notation of the position of each cap is crucial.
https://landroverforums.com/forum/di...rite-up-48197/
https://landroverforums.com/forum/di...rite-up-48197/
The following users liked this post:
Richard Gallant (04-23-2020)
#5

@mollusc I am in the process of deciding how far down this rabbit hole to go, the mains are significantly more work. It largely depends if the new job opportunity pans out, as that will limit my time over the summer which is my only time to do this.
If it does not work out I may do them as well.
If it does not work out I may do them as well.
The following users liked this post:
whowa004 (04-23-2020)
#6

@mollusc I am in the process of deciding how far down this rabbit hole to go, the mains are significantly more work. It largely depends if the new job opportunity pans out, as that will limit my time over the summer which is my only time to do this.
If it does not work out I may do them as well.
If it does not work out I may do them as well.
Not that much more work, and the process is the same, cost is not much more, and beats pulling the oil pan a second time.
Look at my block and you'll see the notches in the bearings and caps(that hold them in place) that Best4x4 was talking about, push the opposite end in first(mains pictured but rods are the same).
You can also remove a rod cap, push the rod up, and use calipers to measure the o.d of the crank, that will tell you if the diameter is stock or oversize.
If you can hang a fingernail on any ridges, lines, or grooves on the crank, then technically, it needs turned.
Hopefully the crank is ok, and the bearings just have normal wear.
Keep in mind that the cam bearings will also likely have the same amount of wear as the crank and rod bearings, so they could potentially make a little noise as well.
I've been stuck in this rabbit hole for a while now too, so wave when you pass by, lol.
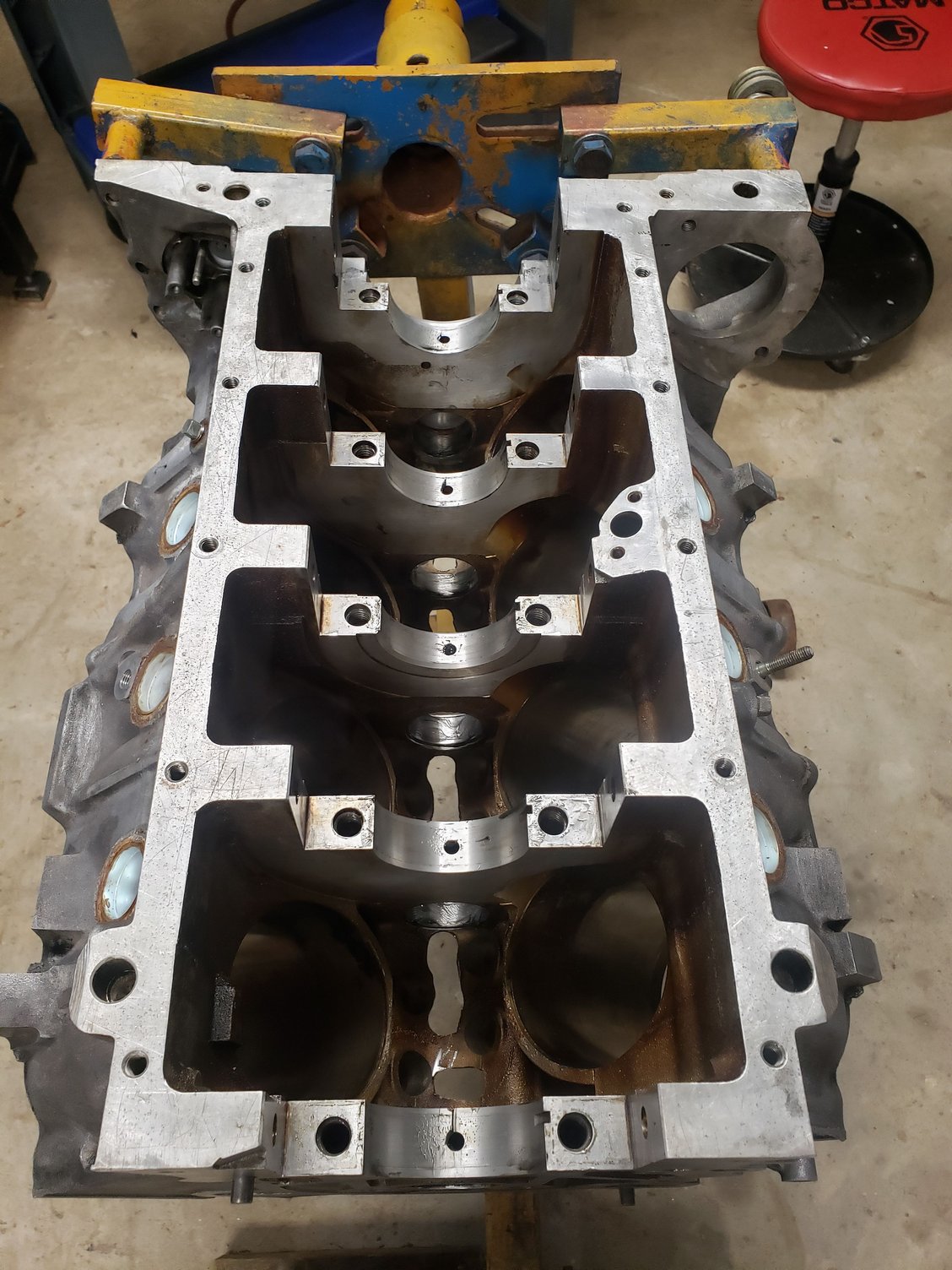
The following 2 users liked this post by Sixpack577:
Richard Gallant (04-23-2020),
whowa004 (04-23-2020)
#7
The following 2 users liked this post by whowa004:
Richard Gallant (04-23-2020),
Sixpack577 (04-23-2020)
#8
The following 2 users liked this post by Sixpack577:
Richard Gallant (04-23-2020),
whowa004 (04-23-2020)
#9
The following users liked this post:
Richard Gallant (04-25-2020)
#10
The following users liked this post:
Richard Gallant (04-25-2020)